Une cinquantaine de visiteurs, de profils variés, ont pris part à la visite du siège et de l’atelier de fabrication d’intras de Starkey, à Créteil, organisée dans le cadre de la Semaine du son. Reportage.
Le fabricant américain avait déjà ouvert les portes de son siège français par le passé mais sans jamais donner à la démarche autant d’ampleur que cette année. Sur la journée, une cinquantaine de personnes de tous horizons sont venus en visite : journalistes, ORL, sophrologue, représentants de sociétés de service dans la réparation d’appareils, déléguée d’une agence du Grand Paris…
Starkey met en avant son histoire
La matinée a commencé par un retour sur l’histoire de l’entreprise, fondée en 1968 par la fusion d’un réparateur toutes marques d’appareils auditifs – le 1er métier de William F. Austin – et d’un laboratoire de fabrication d’embouts sur mesure. La marque Starkey s’est construite sur ce savoir-faire : l’intégration des composants électroniques d’un contour d’oreille de l’époque dans un appareil suffisamment petit pour être positionné dans le conduit auditif. Cette histoire se perpétue, entre autres, dans le fait que Starkey investit 10 % de son chiffre d’affaires dans la R&D. L’entreprise, toujours détenue par son fondateur, compte aujourd’hui 5 500 collaborateurs dans 28 filiales. 140 d’entre eux travaillent au siège de Créteil, avec, a insisté Eric Van Belleghem, directeur marketing, un esprit de famille et une ancienneté très élevée : 18 ans en moyenne. Cette « séniorité » s’explique notamment par le fait que l’entreprise donne la possibilité à ses salariés de monter en compétences et de prendre des responsabilités : « toutes les offres d’emploi sont d’abord proposées en interne », a souligné Eric Van Belleghem. Il a également présenté aux personnes peu familières de l’entreprise, ses actions humanitaires à travers le monde avec la Starkey Hearing Foundation (plus de 1 million d’appareillages en 10 ans) : « voilà pourquoi nous sommes fiers de travailler pour cette entreprise : elle nous donne du sens ».
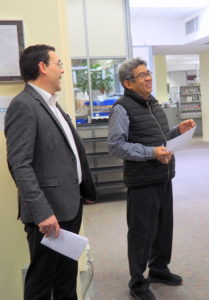
Le directeur technique, Vouthy Toch, ici avec Eric Van Belleghem, fait partie des employés ayant la plus longue ancienneté.
Un parcours normé
La visite s’est poursuivie en 2 groupes conduits par le directeur commercial, d’une part, et par Thierry Gouin, directeur de la satisfaction client, d’autre part,
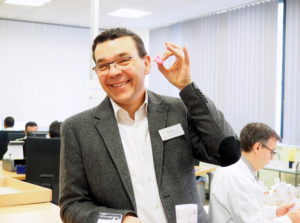
Les empreintes physiques sont encore dominantes mais les fichiers numériques sont de plus en plus nombreux.
au travers des différents espaces de l’unité de production. L’organisation spatiale témoigne de l’histoire de la filiale ouverte en 1981, ce qui en fait l’une des plus anciennes du groupe. Aujourd’hui, le parcours des produits commence dans la surface dédiée à la réception des commandes et à leur saisie. A partir de ce point, une petite boîte, dont la couleur signale le jour de la semaine, va accompagner le produit, qu’il s’agisse de fabriquer un intra-auriculaire sur-mesure ou de procéder à une réparation. D’une manière générale, l’atelier fonctionne avec énormément de signaux visuels pour accompagner la gestion de l’activité. Les objectifs sont clairement affirmés : effectuer au moins 90 % des réparations en moins de 4 jours et 90 % des fabrications en moins de 3 jours, sachant que l’entreprise ne ferme que 2 journées par an pour inventaire. Ces normes internes s’ajoutent naturellement aux obligations de certification Iso qui s’imposent aux fabricants de dispositifs médicaux.
Un savoir-faire cultivé en interne
Deux vastes plateaux sont dédiés d’un côté aux réparations – la demande la plus fréquente est le changement d’écouteur – de l’autre à la fabrication des intras. Celle-ci débute par le scan des empreintes réalisées et expédiées par les audioprothésistes. A l’étape du design, les caractéristiques électro-acoustiques souhaitées sont saisies et l’’agencement interne de l’intra est arrêté. Assurer le gain de place optimal fait partie du cœur du savoir-faire de Starkey France. Un logiciel de suivi assure la traçabilité à toutes les étapes ultérieures : les coques de résine photosensible imprimées en 3D passent sur le plateau de fabrication où les composants électroniques, réceptionnés et préparés par le service logistique, sont insérés. Câblage, gravure du numéro d’identification, assemblage, finitions : chaque étape est chronométrée, avec un système d’auto-contrôle pour éviter les défauts.
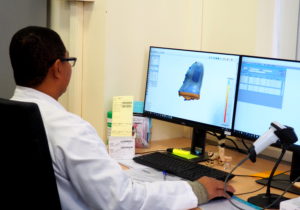
L’opérateur ajoute une fine couche de cire pour gommer les aspérités présentes sur l’empreinte ; il retravaille les zones de rétention et l’étanchéité, fondamentale pour éviter le larsen.
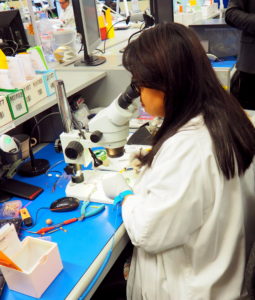
La personne responsable du câblage détermine le bon écouteur pour que l’impédance soit optimale et permette la meilleure restitution du gain offert par l’appareil.
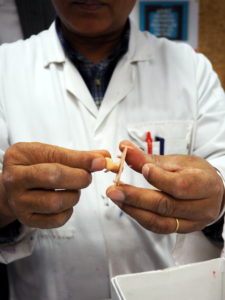
Des opérateurs expérimentés – formés en interne puisqu’il n’existe aucun cursus spécialisé dans le domaine – savent recouper la base de l’intra au plus près, pour le miniaturiser au maximum.
Le service aux audios
Le siège de Créteil gère plus de 500 commandes clients par jour. Une demande de produit standard passée avant 16 heures peut être expédiée le jour-même. Au rez-de-chaussée du bâtiment, à côté de l’accueil, le centre d’appels répond aux questions des professionnels, du fonctionnement du logiciel Inspire aux rectifications de commandes. Les répondants sont souvent d’anciens techniciens de l’atelier ou ayant exercé en centre auditif, par exemple en tant qu’assistants : ils connaissent le quotidien des audios.
Un modèle français
Les intras correspondent à 35 à 40 % de l’activité de Starkey en France, bien au-dessus de la part de marché actuelle de cette catégorie dans les ventes, tous fabricants confondus (7-8 %). Sans surestimer l’importance que ce type d’appareils aura à l’avenir, l’équipe dirigeante française reste convaincue qu’il s’agit d’un produit différenciant pour les audioprothésistes et investit massivement dans leur formation et la reconnaissance de leur savoir-faire, via le label Maître Audio. Au niveau mondial, les innovations technologiques continuent à être déclinées dans des modèles intras, sans négliger les spécificités des marchés régionaux (Starkey est implanté dans 100 pays), par exemple la part du rechargeable en France. Par son positionnement, le fabricant réaffirme sa volonté d’épouser le modèle de distribution actuel. « Toutes les data montrent que la réussite de la réhabilitation auditive dépend du suivi par un professionnel de l’audition, rappelle Eric Van Belleghem. Forts de cette connaissance, nous réfléchissons aux outils permettant aux audios de répondre à la demande des malentendants et de leur apporter le plus haut niveau de satisfaction. »